

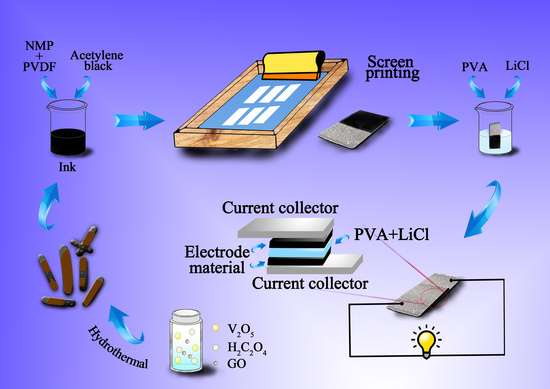
However, only ~1 to 2% of lignin is isolated from wood pulp for commercial applications, the majority is burned onsite for heat and pulping chemical recovery. The kraft process is the most widely used pulping process and kraft lignin accounts for more than 90% of the world’s chemical pulp lignin production. More than 70 million metric tons of lignin are produced annually as a byproduct from wood delignification and pulping processes.

Lignin is the second major component of lignocellulosic biomass and the most abundant aromatic biopolymer resource on Earth. However, there have been limited studies on the use of wood or agricultural biomass as the carbon source to produce graphene-based materials. Biomass presents an abundant and low-cost source of carbon. The challenges of sustainable development have driven people to find facile, environmentally friendly ways to produce carbon-based materials. The critical parameters, including heating temperature, heating time, and particle sizes of the Fe-lignin composites, have been explored to understand the graphene formation mechanism and to obtain the optimized process parameters to improve the yield and selectivity of graphene materials. The graphene shells are peeled off the metal core and simultaneously welded and reconstructed to graphene materials under a selected welding reagent. Then, these graphene-encapsulated metal structures are opened by the molecule cracking reagents. It involves preparing metal (M)-lignin nanocomposites from kraft lignin and a transition metal catalyst, pretreating the M-lignin composites, and forming of the graphene-encapsulated metal structures by catalytic graphitization the M-lignin composites. MCW process is a low-cost, scalable technique to fabricate few-layer graphene materials. The increased electrical conductivity of the final composite may enable potential electronic applications.In this work, few-layer graphene materials were produced from Fe-lignin nanocomposites through a molecular cracking and welding (MCW) method.
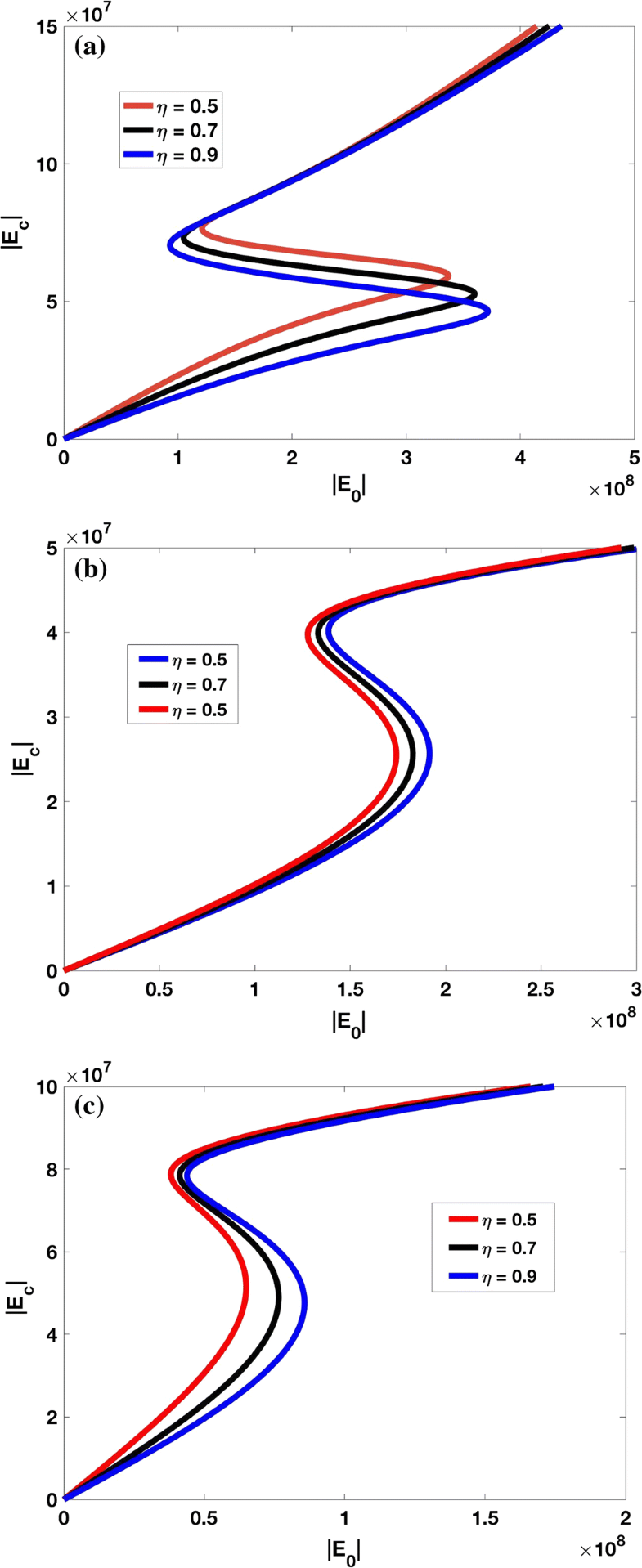
Electrical conductivity investigation using a four-probe resistivity measurement system showed that PANI addition to the composite not only enhanced the interfacial interaction but also improved the electrical conductivity of the composite. The thermal stability of the composites was also improved compared to that of neat PS. Thermal investigation showed that the addition of GO to the PANI-coated PS increased the glass transition temperature of the PANI-PS/GO composites. The existence of PANI in the PS and PS/GO core shell composite was confirmed by the appearance of a new peak in the photoelectron spectroscopy and energy-dispersive X-ray spectroscopy results assigned to the nitrogen band. GO could be easily coated on PANI-coated PS to form a PANI-PS/GO core shell structure through the ring-opening reaction of the epoxide groups in the GO sheets with amine groups in the PANI nanofibers. A simple method was used to synthesize the polyaniline nanofiber-coated polystyrene/graphene oxide (PANI-PS/GO) core shell composite using a solution mixing process.
